Anodizing process
Anodizing is an electrochemical surface treatment process that can be used to surface treat aluminum and other metals to enhance their corrosion resistance and hardness. The following is the general anodizing process:
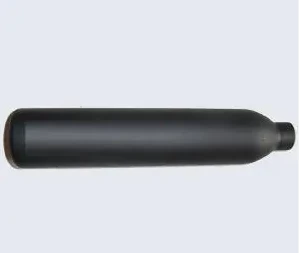
Cleaning: Before anodizing, metal parts need to be cleaned to remove surface grease and impurities. The cleaning process is usually carried out with an alkaline or acidic solution.
Pre-treatment: Metal parts are first subjected to some pre-treatment, such as deburring, grinding or polishing. This can improve the surface finish after anodizing to a certain extent.
Electrolyte: Metal parts are placed in an electrolyte containing oxidants and other additives. The composition of the electrolyte depends on the metal used and the desired surface treatment.
Current and time: By adding a DC current to the electrolyte, the metal part becomes the anode. The current and processing time are adjusted according to the desired processing effect.
Anodizing: In the electrolyte, an oxide film is formed on the surface of the metal part, a process known as anodizing. In this process, the thickness and color of the oxide film depend on the electrolyte used and the current/time parameters.
Sealing: By soaking in hot water or other sealants, the micropores of the oxide film are sealed, thereby enhancing its corrosion resistance and hardness.
Washing and drying: Processed parts need to be washed and dried to remove excess electrolyte and sealant.
In general, anodizing is a multi-step process that requires careful handling and control of the parameters of each step to achieve the desired surface treatment.