Forgeage à froid : avantages et applications dans la fabrication
Dans le domaine du travail des métaux, le forgeage à froid est considéré comme une technique remarquable qui allie précision, solidité et efficacité. Contrairement au forgeage à chaud, le forgeage à froid utilise une pression et une force mécaniques à température ambiante pour façonner et transformer les métaux en pièces complexes. Des composants automobiles aux applications aérospatiales, le processus a trouvé de nombreuses applications dans diverses industries. Dans cet article de blog, nous plongeons dans le monde du forgeage à froid et explorons ses avantages, ses applications et les facteurs qui contribuent à son succès. Le forgeage à froid est une méthode flexible et efficace processus de fabrication qui offre de nombreux avantages tels que des propriétés mécaniques améliorées, une précision dimensionnelle, une conservation des matériaux et la possibilité de fabriquer des pièces complexes. Ses applications couvrent une grande variété d’industries, ce qui en fait une technique importante dans le travail des métaux moderne.
Processus de forgeage à froid
Le processus de forgeage à froid comporte plusieurs étapes qui permettent la mise en forme et le formage du métal à température ambiante. Voici un aperçu du processus typique de forgeage à froid :
- Sélection des matériaux : Le processus commence par la sélection d’un métal approprié pour le forgeage à froid. Les métaux ayant une bonne ductilité, tels que l’acier, l’aluminium et les alliages de cuivre, sont couramment utilisés en raison de leur capacité à résister à la déformation sans se fissurer.
- Préparation des billettes : Le métal choisi est obtenu sous forme de billette cylindrique. La billette est généralement prédécoupée à la longueur et au diamètre souhaités, en fonction des spécifications de la pièce finale.
- Lubrification: La lubrification est essentielle en forgeage à froid pour réduire la friction entre le métal et les outils de forgeage. Il permet une déformation plus facile du métal et permet d’éviter une usure excessive des outils. Les lubrifiants aident également à éliminer les pièce forgée de la matrice après le processus.
- Conception des matrices : Une matrice, composée de deux moitiés, est conçue pour épouser la forme souhaitée de la pièce finale. La matrice contient des cavités et des caractéristiques qui confèrent au métal la forme, les dimensions et les détails souhaités pendant le processus de forgeage. La matrice est généralement fabriquée en acier trempé pour résister aux pressions élevées impliquées.
- Opération de forgeage : La billette lubrifiée est placée dans la cavité de la filière. Une presse mécanique exerce une pression élevée sur la billette, la déformant et prenant la forme de la matrice. La pression appliquée peut aller de plusieurs tonnes à plusieurs milliers de tonnes, selon la taille et la complexité de la pièce. La force de pression est généralement appliquée de manière progressive pour assurer un remplissage correct de la cavité de la matrice et minimiser les défauts.
- Opérations de finition : Après le forgeage initial, des opérations supplémentaires peuvent être réalisées pour affiner la forme et les dimensions de la pièce. Ces opérations peuvent inclure la coupe du matériau en excès, le perçage de trous, le frappe (création de motifs en relief) ou d'autres processus de formage secondaires. Les opérations de finition permettent d'obtenir la forme finale souhaitée et la précision dimensionnelle de la pièce.
- Traitement thermique (facultatif) : Dans certains cas, les pièces forgées à froid peuvent subir des processus de traitement thermique, tels que le recuit ou la trempe, pour améliorer leurs propriétés mécaniques et éliminer les contraintes résiduelles.
- Traitement de surface (facultatif) : En fonction des exigences et de l'application de la pièce, des traitements de surface tels que le placage, le revêtement ou la peinture peuvent être appliqués pour améliorer la résistance à la corrosion, l'esthétique ou d'autres propriétés fonctionnelles.
- Inspection et contrôle qualité : Les pièces finies forgées à froid sont soumises à des mesures d’inspection et de contrôle qualité approfondies pour garantir qu’elles répondent aux spécifications et normes requises. Cela peut inclure des contrôles dimensionnels, des tests de dureté, une inspection visuelle et d'autres méthodes de tests non destructifs ou destructifs.
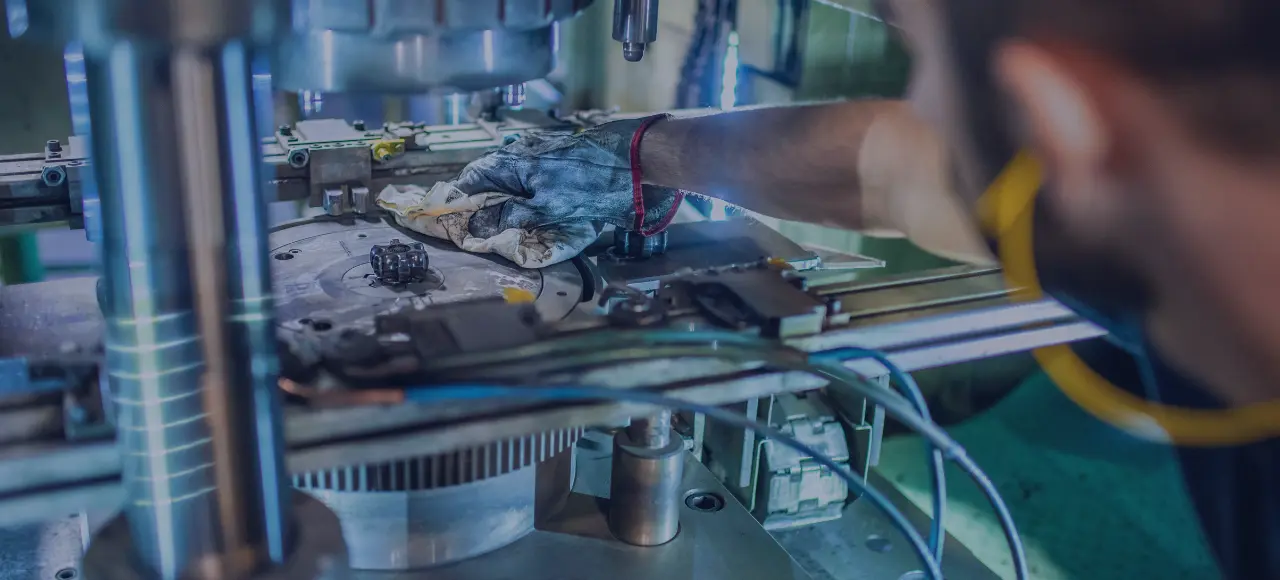
Avantages du forgeage à froid
- Propriétés mécaniques améliorées : Le forgeage à froid permet d’obtenir des pièces aux propriétés mécaniques supérieures. Le processus affine la structure des grains du métal, conduisant à une résistance, une ténacité et une résistance à l'usure accrues. Ces propriétés rendent les composants forgés à froid très recherchés pour les applications où la fiabilité et la durabilité sont primordiales.
- Précision dimensionnelle et finition de surface : Le forgeage à froid facilite la création de formes complexes et de tolérances serrées avec une précision exceptionnelle. L'absence de températures élevées empêche la déformation du matériau et permet des détails plus fins. De plus, le processus donne d’excellents états de surface, réduisant ainsi le besoin d’usinage ou de polissage supplémentaire.
- Conservation du matériel : Le forgeage à froid minimise le gaspillage de matière par rapport au forgeage à chaud. Sans avoir besoin de températures élevées, il n’y a pas de formation de tartre ni d’oxydation, ce qui réduit la perte de matière. Cela fait du forgeage à froid un choix écologique et rentable.
- Production de pièces complexes : La polyvalence du forgeage à froid permet la création de pièces complexes qui seraient autrement difficiles à fabriquer. La haute pression appliquée lors du forgeage à froid permet de réaliser des géométries complexes, notamment des caractéristiques internes, des filetages et des contre-dépouilles. Cela ouvre de nouvelles possibilités aux concepteurs et aux ingénieurs, permettant ainsi des conceptions de produits innovantes et efficaces.
Applications du forgeage à froid
- Industrie automobile : Les composants forgés à froid jouent un rôle crucial dans le secteur automobile. Des pièces de moteur et de transmission, telles que les engrenages, les arbres et les roulements, aux composants du système de suspension et de direction, comme les tirants et les rotules, le forgeage à froid offre des solutions hautes performances. La résistance et la précision des pièces forgées à froid contribuent à améliorer la sécurité, le rendement énergétique et la fiabilité globale des véhicules.
- Aéronautique et Défense : Dans l'exigence aérospatiale et défense Dans les secteurs où la fiabilité et la réduction de poids sont primordiales, le forgeage à froid est largement utilisé. Les composants de moteurs d'avion, les pièces de train d'atterrissage, les fixations et les composants de missiles ne sont que quelques exemples d'applications qui bénéficient de la résistance et de la précision dimensionnelle exceptionnelles obtenues grâce au forgeage à froid.
- Industrie électronique et électrique : Le forgeage à froid est utilisé dans la production de connecteurs électriques, de bornes et d'autres pièces complexes pour l'industrie électronique. Les capacités de mise en forme précises du forgeage à froid garantissent une conductivité électrique, une stabilité mécanique et une fiabilité à long terme optimales.
- Construction et infrastructures: Les boulons d'ancrage, les fixations et les composants structurels forgés à froid trouvent leur place dans les projets de construction et d'infrastructure. La haute résistance et la précision dimensionnelle fournies par le forgeage à froid garantissent l'intégrité structurelle, la durabilité et la facilité d'installation.