what is the Anodic oxidation
Gary Young
baidu
2023-08-09 10:51:53
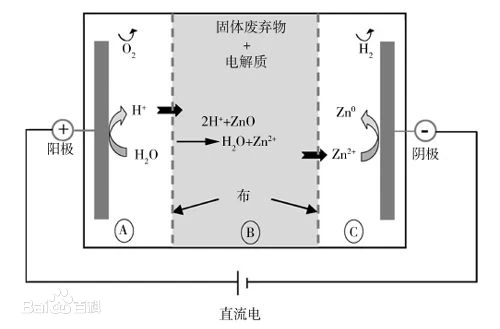
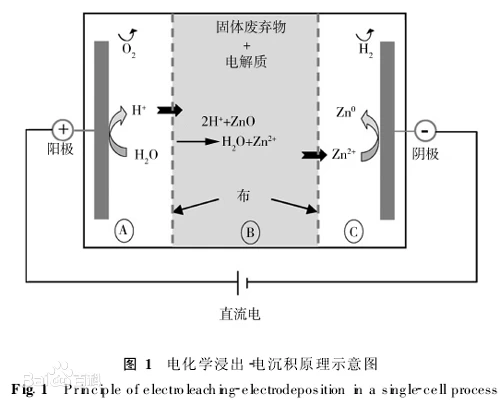
In order to overcome the defects of aluminum alloy surface hardness, wear resistance, etc., expand the scope of application, and extend the service life, surface treatment technology has become an indispensable part of the use of aluminum alloy, and anodizing technology is the most widely used and successful.
Chinese name: anodic oxidation, foreign name: anodic oxidation, interpretation, electrochemical oxidation of metals or alloys, usually refers to the anodic oxidation phase of sulfuric acid cathodic reduction, see the journal "Chemical Terms" Science Press, published in 1991 [3]
directory
1 Principle
2 Other types
3 Role
4 Differences
Principle Edit Broadcast
The so-called anodizing of aluminum is an electrolytic oxidation process in which the surface of aluminum and aluminum alloys is usually transformed into an oxide film that has protective, decorative and other functional properties. The anodizing of aluminum from this definition only includes the part of the process of generating an anodizing film.
The metal or alloy parts are used as anodes, and the surface of the oxide film is formed by electrolysis. Metal oxide films change surface conditions and properties, such as surface coloring, improving corrosion resistance, enhancing wear resistance and hardness, and protecting metal surfaces. For example, aluminum anodizing, aluminum and its alloys are placed in the corresponding electrolyte (such as sulfuric acid, chromic acid, oxalic acid, etc.) as anodes, under specific conditions and applied current, electrolysis. The aluminum or its alloy of the anode is oxidized, and a thin layer of alumina is formed on the surface, with a thickness of 5~30 microns, and a hard anodizing film can reach 25~150 microns. Anodized aluminum or its alloy, improve its hardness and wear resistance, up to 250 ~ 500 kg / square millimeter, good heat resistance, hard anodized film melting point up to 2320K, excellent insulation, breakdown voltage up to 2000V, enhanced corrosion resistance, in ω = 0.03NaCl salt spray after thousands of hours of no corrosion. There are a large number of micropores in the thin layer of oxide film, which can adsorb various lubricants and are suitable for manufacturing engine cylinders or other wear-resistant parts; The membrane has strong microporous adsorption capacity and can be colored into a variety of beautiful and bright colors. Non-ferrous metals or their alloys (such as aluminum, magnesium and their alloys, etc.) can be anodized, this method is widely used in mechanical parts, aircraft parts, precision instruments and radio equipment, daily necessities and building decoration. [1]
Generally speaking, the anode is made of aluminum or aluminum alloy as the anode, and the cathode is selected from the lead plate, and the aluminum and lead plate are placed together in an aqueous solution, which has sulfuric acid, oxalic acid, chromic acid, etc., for electrolysis, so that the surface of the aluminum and lead plate forms an oxide film. Among these acids, the most widespread is anodizing with sulfuric acid.
Other types of editing announces
In addition to metals, the oxidation caused by other substances as anodes is also called "anodic oxidation".
In the real process, anodizing for aluminum alloys is more, which can be applied in daily life, so that the characteristics of this process make the surface of aluminum parts produce a hard protective layer, which can be used to produce daily necessities such as kitchenware. However, the anodizing effect of cast aluminum is not good, the surface is not bright, and it can only be black. Aluminum alloy profiles are a little better.
Role Editing Broadcast
Protection
Decorative
Insulation
Improved adhesion to organic coatings
Improved adhesion to inorganic overlays
Other features in development
Differentiating Editing Announces
The difference between anodic oxidation and conductive oxidation
1) Anodizing is carried out under the condition of high voltage electricity, which is an electrochemical reaction process; Conductive oxidation (also known as chemical oxidation) does not need to be electrified, only needs to be soaked in the potion, it is a pure chemical reaction.
2) Anodoxidation takes a long time, often tens of minutes, while conductive oxidation only takes a few tens of seconds.
3) The film generated by anodic oxidation has several microns to dozens of microns, and is hard and wear-resistant; The film generated by conductive oxidation is only 0.01-0.15 microns, and the wear resistance is not very good, but it can conduct electricity and resist atmospheric corrosion, which is its advantage.
4) The oxide film is originally non-conductive, but because the film generated by conductive oxidation is really thin, it is conductive.